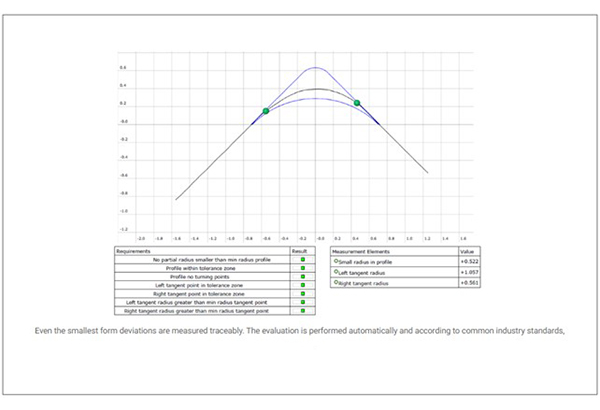
A new approach to the optical inspection of turbine blades
Working with the leading manufacturers, we have become expert in aircraft engines and other gas turbines. Blades are measured when newly manufactured, after testing and to assess wear patterns. This process enables replacement on condition. Being specialist in this field, we can assess parameters including
- Cooling hole geometry
- Airfoil analysis (leading and trailing edge radii, form deviation, profile twists)
- Fir tree geometry
- Profile and areal roughness
- Defects and wear
A future-proof solution
The Alicona G6 with Real 3D rotation unit is ideal for the rapid measurement of the geometry and surface roughness of high value components.
Recent developments include
- Vertical Focus Probing – the optical probing and measurement of holes (such as cooling holes) and vertical flanks
- SmartFlash – designed to ensure high resolution measurement of smooth, reflective and highly polished surfaces
- 5 axes metrology – the high precision rotation unit allows measurement of complex geometries, enabling capture of GD&T data and roughness parameters on an entire object
The G6 is in regular use at several European facilities measuring turbine blades both when manufactured and when removed for evaluation at end of life.
The Alicona G6 with Real 3D rotation unit
The G6 being the latest in a long line of products from Alicona, uses focus variation coupled with a sample mount capable of positioning the sample in 3 dimensions. It will measure to sub micron accuracy, combining the functionality of a roughness measuring system with a coordinate measuring machine.