“Optimax have an extensive product range that was very attractive to us. They took the time to understand my requirements and align a solution that fitted into my manufacturing processes. They were very knowledgeable and friendly, I found the virtual demonstration extremely helpful. The outcome of the project has been very successful and performs above expectations. I would definitely recommend Optimax.”
“For over 14 years Optimax has been providing us with inspection equipment, service and most importantly expertise. We need suppliers that can go the extra mile in looking specifically at our application and then providing a suitable and sometimes bespoke solution, and this is where Optimax have really made a difference”.
“Optimax are a trusted partner! We have been working in partnership with Optimax for several years, to supply us with inspection solutions, service, and onsite calibration to UKAS standards. Their knowledge and expertise is exceptional, they provide honest, independent advice. Optimax are quick to provide options and solutions for our inspection requirements. They work hard to deliver a solution that 100% fits the application rather than just supplying a product. Optimax work with us to ensure we achieve our inspection objectives – they are one of the first companies I turn to.”
“The Optimax team with their extensive knowledge and expertise, have proven themselves to be the ideal partner for independent, candid advice. They are a company we can trust to support our metrology and visual inspection needs whether we are purchasing equipment or developing specific metrology instruments for our applications. Their experience and methodical attention to detail mean the outcomes we achieve support our testing requirements”.
Accreditations
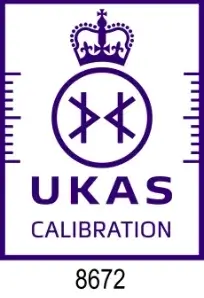
UKAS
Calibration under UKAS 17025 for
profile projectors and many types of microscopes.
ISO10360-7 for UKAS calibration of
optical CMM’s with imaging probing systems.
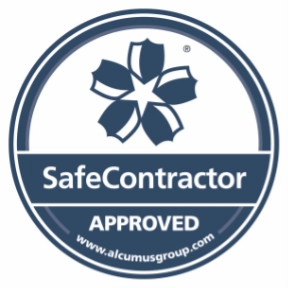
Alcumus Safe Contractor
SafeContractor approved for the assurance
of quality and verified good practice, in
Service and Calibration of Optical Measuring
Instruments.
Service & Calibration
We are calibration experts, UKAS accredited since 2015, our lab is assessed to ISO 17025. We are pioneering in our approach, the first lab in Europe to win approval for ISO10360-7 CMM’s fitted with optical probes aka Vision systems, and more recently Optical shaft measuring. But our engineers don’t just calibrate, they clean, adjust and make minor repairs to your instruments as part of the standard calibration visit, ensuring continued best performance. If parts or more extensive repairs are needed, we will provide a detailed quote. Field engineers are supported by a dedicated customer care team, keeping track of your calibration assets and letting you know when visits are due. We will always try and provide not only a best commercial package, but also a service as standard to go along with the calibration, from the industry’s friendliest team.
We ‘re here to help you…
Bespoke solutions to your
individual application challenges,
designed with precision, efficiency
and productivity in mind.
Visit our resources centre to learn
more about our work.
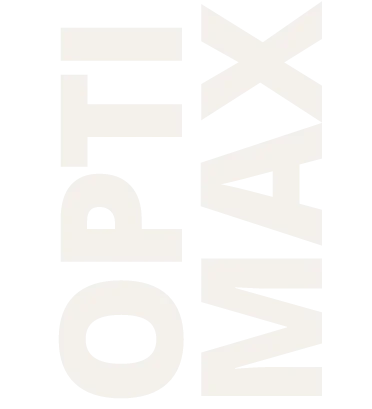
Why Optimax
Discover the benefits of latest generation optical inspection and
metrology solutions. Our aim is simple, to ensure your organization’s
inspection and measurement is accurate reliable and repeatable,
on time, every time.
Calibration & Services
We believe that purchasing equipment is just the start of the journey.
We offer accredited calibration and service, training and repair packages
specifically tailored to your ongoing requirements.
Technical Experts
Our Engineering and Technical Sales teams have a wide-ranging
skill set, designed to deliver intelligent solutions for production
metrology and inspection.
We’re here to help - get in touch
Calibration & Services
Keeping your business up and running 24/7, with a range of calibration and service packages tailor-made to your requirements.
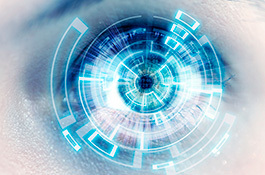
Why Optimax
Passion, Innovation, and Experience help us improve accuracy, quality, and efficiency, ensuring your inspection and measurement is reliable and repeatable, on-time, every time.
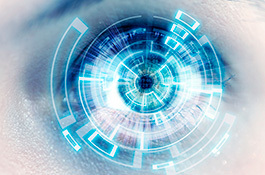
Technical Experts
People are at the heart of our business, we have the skills, knowledge, and know-how to provide you with independent advice and support.
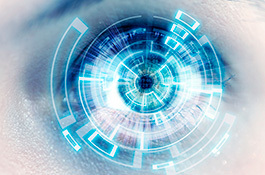