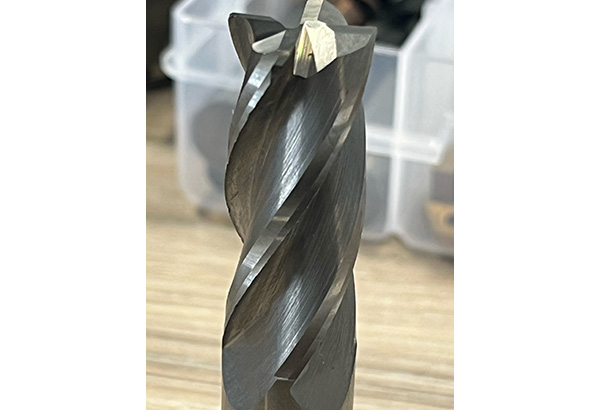
Helping IMCO solve the time old challenge of reducing machining times
IMCO are known for their high-quality cutting tools, and the accuracy and repeatability of edge preparation and honing are important; other parameters that provide additional information, such as shape, contour accuracy, rake angle, undercuts, chipping, and roughness on the chip surface. As IMCO offers milling cutters with up to thirteen flutes that achieve above-average surface finish, these features are critical to performance. They came to us seeking a way to shorten machining times and extend the service life of cutting tools, a problem shared with users and manufacturers.
Reduced time required for measurements by 75%
There are ever-increasing customer demands for tolerance and performance. As new applications and materials that need machining are developed, these parameters change and must be monitored including roughness measurement, GD&T measurement (form/geometry), cutting-edge geometry, defect measurement, wear measurement, coating measurement, and integrity.
We recommended that IMCE used the Bruker Alicona EdgeMaster series includes the Edge Master, EdgeMasterX and EdgeMasterHOB tool measuring systems. The measuring systems are used for high-resolution, fully automatic measurement of tool cutting edges in production.
With the EdgeMaster, users measure radii >2μm and rake, wedge, and clearance angle of tools. Different types, including both waterfall and trumpet, are precisely measured. Traceable and repeatable results are delivered in high vertical resolution even at vibrations, variations in temperature and ambient light. In addition to chipping measurement, the high vertical resolution enables traceable roughness measurement on the rake face. Implementing the EdgeMaster on the factory floor, IMCO reduced the time required for measurements by 75%, resulting in a rapid ROI.
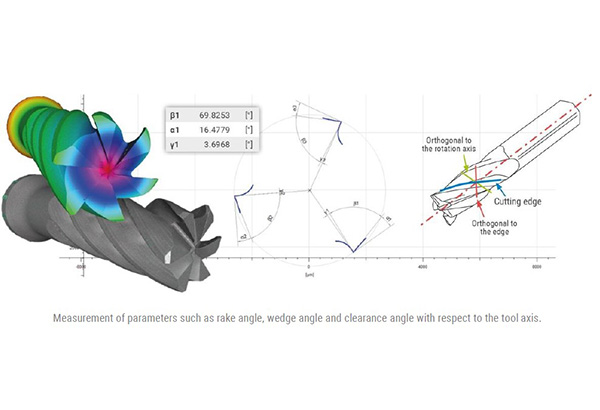
The Bruker Alicona EdgeMaster
The Bruker Alicona EdgeMaster series includes the Edge Master, EdgeMasterX and EdgeMasterHOB tool measuring systems. The measuring systems are used for high-resolution, fully automatic measurement of tool cutting edges in production. Whether you use an EdgeMaster in the measuring room or on the shop floor does not change the result: The measurements are high-resolution and robust even in the presence of vibrations, extraneous light, and temperature fluctuations.
With the EdgeMaster, users measure radii >2μm and rake, wedge, and clearance angle of tools. Different types, including both waterfall and trumpet, are precisely measured. Traceable and repeatable results are delivered in high vertical resolution even at vibrations, variations in temperature and ambient light. In addition to chipping measurement, the high vertical resolution enables traceable roughness measurement on the rake face. By implementing the EdgeMaster on the factory floor, IMCO could reduce the time required for measurements by 75%, resulting in a rapid ROI.