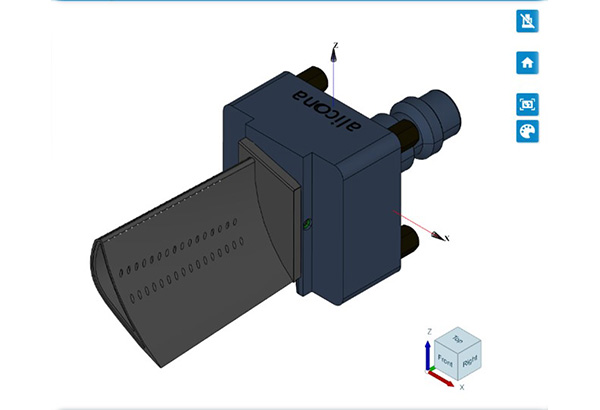
We know the limits of conventional metrology techniques
Turbine engines operate under increasingly elevated temperatures for maximum exhaust velocity and optimum efficiency. Internal temperatures reach up to 2000°C and exceed the melting point of turbine blades. An advanced cooling system with up to 500 specially shaped cooling holes is made through the turbine blades to prevent self-destruction. These holes circulate a thin, turbulent layer of air between the combustion gases and blades. They are essential for safe, long-term use of the engine. Each cooling hole must conform to the angle, size, position, and shape design. Conventional metrology techniques do not provide the solution for internal hole measurement in terms of geometry and finish, especially where the hole entry geometry is complex with tapered entry points, as shown below.
Partial light offers a stand out solution
The Bruker Alicona optical Focus Variation technique with Vertical Focus Probing now solves these measurement challenges. This technique allows holes with depth-to-diameter ratios up to 10-1 to be internally measured. Vertical Focus Probing is based on the use of partial light. This means that light from different directions is used in addition to coaxial light. As a result, the objective captures individual light rays diffusely reflected from vertical surfaces again, enabling the traceable and repeatable measurement of flanks with more than 90° in high resolution.
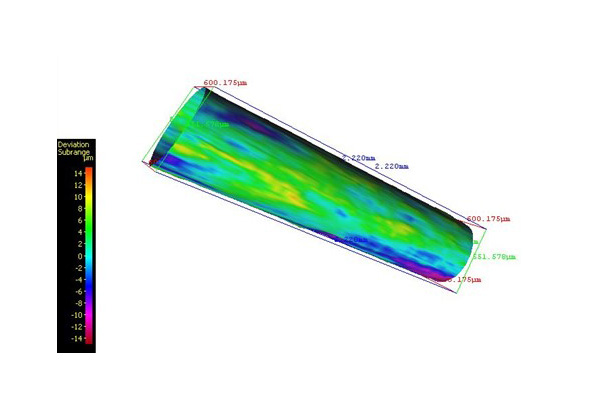
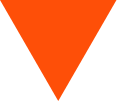
Bruker Alicona µCMM
Bruker Alicona’s µCMM stands as a pinnacle in optical metrology. Designed for micron-level accuracy, it offers unparalleled precision in measuring complex geometries and surface topographies. Employing advanced microscopy techniques, µCMM ensures superior quality control.Vertical Focus Probing enables measurement in holes with varying geometries down to 400µm. Full automation is available using the MetMax software. To demonstrate the capabilities of the Vertical Probing technology Optimax created a test plate with a series of holes representing typical cooling holes. The plate was mounted in an Advanced 3D Rotation Unit on a Bruker Alicona µCMM (coordinate measuring machine), and the scanning started. The first parallel hole has a diameter of 534 µm and a length of 2.2 mm. The second tapered entry hole demonstrates the ability to measure shaped hole geometry and perform measurements along its entire length.